1.受注から納品までの進捗を全従業員が把握する一元システム
当社では、全従業員が進行状況をひと目で把握できる一元システムを導入しています。見積もりは担当制で複数人が行うことで見積スピードをあげていますが、その際、社内の品物の各納期が見えていますので、すぐに納期回答することができます。必要に応じて各品物の作業手順をフレキシブルに変更し、可能な限りお客さまの要求納期に応える体制を構築しています。
納期から逆算して最適な工程をシステムに入力するだけではなく、各工程の担当者が進行を把握し、後工程の状況を確認しながらスケジュールを調整します。
2.要求精度を実現する工程設計
難しい案件については、お客さまから図面をいただいた時点で「どこの精度がより重要か」という点についてディスカッションいたします。精度要求が複数ある場合でも、新しいアイデアでベンダー金型の製作や、複数部品に分けて溶接など、お客さまの要求を満たすご提案をいたします。
求める精度によって、加工方法も変わってきます。たとえば1枚の板に多くの絞りや孔が開いている場合、加工の順番が重要になります。絞ると周囲の金属が引っ張られ歪んでしまいます。歪むであろう場所に孔や、他の絞りがある場合は歪みを生じさせない手順を考える必要があります。
3.不良の定義を明確にし、不良は後工程へ送らない
不良の定義は会社によって異なります。まずは社内で、どういったものが不良になるかという定義を明確にすることが重要です。
当社では、バリや材料のキズも不良の一つとみなし、後工程に不良を渡さないことを徹底しております。例えば、バリの取り漏れがあった場合は、受け取った作業者が責任を持って前工程の作業者へ戻します。
4.顧客からのフィードバックを重要視する
お客さまからのフィードバックは良いことも、改善点も含めて作業者へフィードバックし、常によりよい方法を探します。また、似たような加工を検索できるように、過去の製作履歴はデータベース化して、そのデータベース内にお客さまからのフィードバックも入れることで、後から見ても、その仕事に対してお客さまがどのような評価を行ったのかを閲覧できるようになっています。
5.目的を把握し、提案を行う
それでも実際には、「実現が難しい」形状や精度の問題はあります。その場合でも、「できません」とは言わず、お客さまとのコミュニケーションを通じて「解」を求める努力をいたします。私達のコンセプト「アジリティ」とはただ速い精密板金ではなく、お客さまの状況に応じて最適な答えを生み出していくフレキシブルさでもあります。
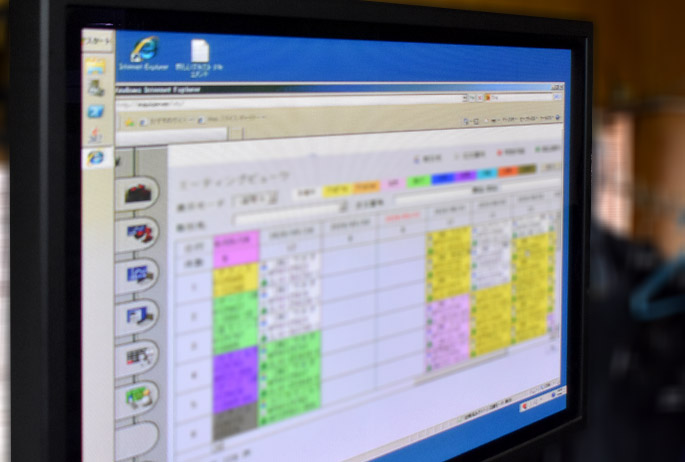
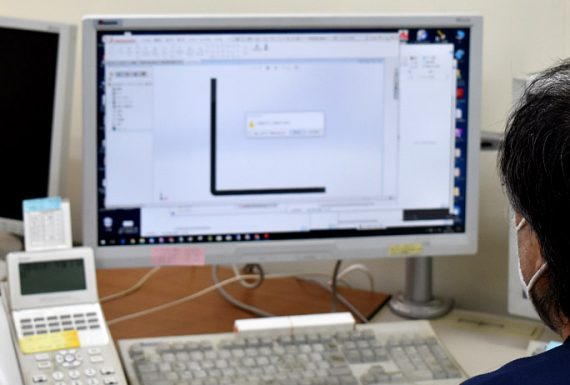
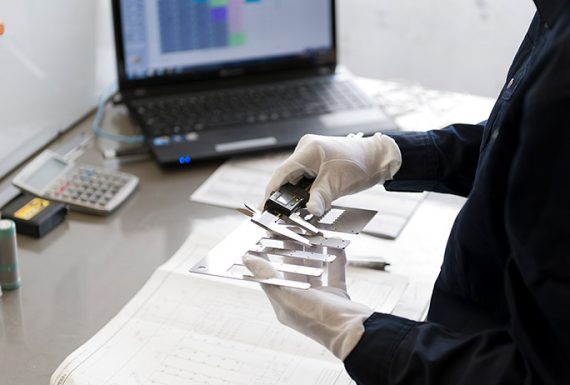
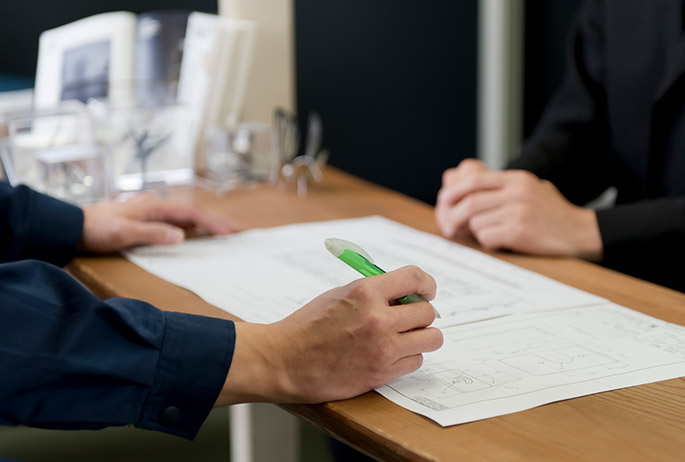